
- Spur and helical gear design generator#
- Spur and helical gear design full#
- Spur and helical gear design download#
To receive a course demo, click on the button below. Helical gears are less efficient because they have more teeth touching when two gears are connected, resulting in increased friction and more energy loss due to heat. Spur gears are more efficient.įor more information on these gears, go through Gear Classification and Terminology: Spur and Helical Gears. This also increases the stress on the gear teeth. Each time a gear tooth engages a tooth on the other gear, the teeth collide, creating noise. Helical gears are more durable than spur gears because the load gets distributed across more teeth. Hence, for a given load, the force will be spread out better than with a spur gear, resulting in less wear on individual teeth. Helical gears are capable of holding more load compared with spur gears, because the load is distributed across more teeth. This fact makes spur gears simpler in design and easier to create than a helical gear, leading to a decreased cost of production.
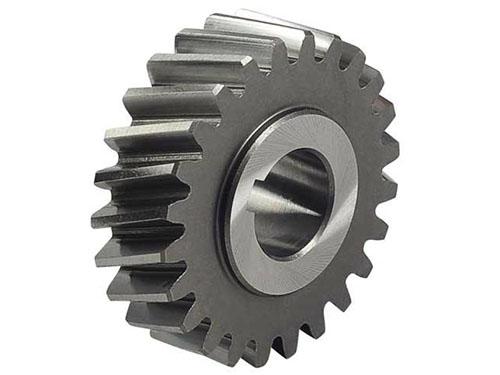
Spur gears have straight teeth, and are mounted on parallel shafts. Spur gears are usually the first choice when exploring gear options, as they are easily manufactured and less cost is involved to manufacture them compared to helical gears.
Spur and helical gear design full#
When two teeth on a helical gear system engage, the contact starts at one end of the tooth and gradually spreads as the gears rotate, until the two teeth are in full engagement. The teeth on helical gears, however, are cut at an angle to the face of the gear. The teeth of a spur gear are exactly perpendicular to its flat faces. Teeth are projected radially and are parallel to the axis of the gear. Here are some additional differences between these two gears.Ī spur gear can be identified by its teeth. Look as hard as you like, but you won’t find spur gears in your car! Helical gears are used in almost all car transmissions. Helical gears, on the other hand, operate much more smoothly and quietly than spur gears. Spur gears are used in many devices, like the electric screwdriver, wind-up alarm clock, and washing machine. S pur and helical gears are two different types of mechanical gears falling under the category of “gears for parallel shafts”. For example, there are gears for parallel shafts, gears for intersecting shafts, and gears for skewed shafts. Thi make gear de ign quite im- pie (almost like electing fa tener ), economical, and available for e eryone, reducing tooling expense and inventory. Kleiss Introduction odem gear de ign i generally based on tandard tool. Must be reduced for teeth with a 25-degree pressure angle having a clearance in excess of 0.250/P.Gear types can be classified according to the relative position of their axes of revolution. Direct Gear Design for Spur andHelicalInvoluteGears Alexander L Kapelevich and Roderick E. This should be avoided on highly loaded gears where the consequently reduced J factor will increase gear tooth stress excessively.ī A minimum clearance of 0.157/P may be used for the basic 20-degree and 25-degree pressure angle rack in the case of shallow root sections and use of existing hobs or cutters.Ĭ The fillet radius of the basic rack should not exceed 0.235/P for a 20-degree pressure angle rack orĠ.270/P for a 25-degree pressure angle rack for a clearance of 0.157/P. This is of particular importance on gears of few teeth or if the gear blank configuration requires the use of a small diameter shaper cutter, in which case the dedendum may need to be increased to as much as 1.45/P. Spur Gear design formula for geometry, pitch, tooth clearance and critical functional data.Įquations for Standards Spur Gears To Findįormulas for Tooth Parts, 20-and 25-degree Involute Full-depth TeethĪNSI Coarse Pitch Spur Gear Tooth Forms ANSI B6.1 To CalculateĮquations Tooth Parts, 20-and 25-degree Involute Full-depth Teeth ANSI Coarse Pitch Spur Gear Tooth Forms ANSI B6.1Ī When gears are preshave cut on a gear shaper the dedendum will usually need to be increased to 1.40/P to allow for the higher fillet trochoid produced by the shaper cutter.
Spur and helical gear design download#
Spur Gear and Assembly Builder - Download DXF, SVG ***
Spur and helical gear design generator#
Spur Gear Calculator and Geometry Generator - Download DXF, SVG, csv file.
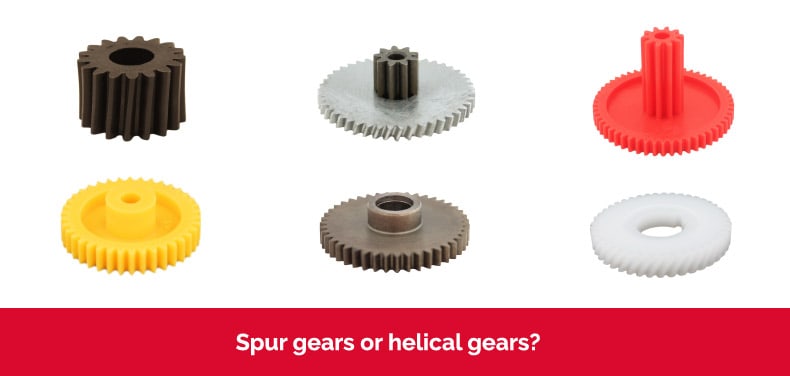

